Labbe Heavy Industries
CNC Wheel Bead Cutting
CNC Wheel Bead Cutting
Couldn't load pickup availability
- Bead cut on Alcoa style wheels 22.5" to 22"
- Bead cut on Alcoa style wheels 24.5" to 24"
- Bead cutting can be performed on new or used rims as requested
* Used rims must be pressure washed clean + stems removed
--
Understanding CNC Wheel Bead Cutting
The Importance of Wheel Beads
Wheel beads are the edges of the wheel rim where the tire bead seats. Properly cut wheel beads are essential for ensuring a tight fit between the tire and the wheel, which is crucial for maintaining tire pressure, preventing air leaks, and ensuring safe driving conditions. The precision in cutting wheel beads directly impacts the overall performance and safety of the vehicle.
CNC Technology in Wheel Bead Cutting
How CNC Machines Work
CNC machines are automated milling devices that utilize computer programming inputs to operate. These machines follow a set of coded instructions, often referred to as G-code, which dictate the movements of the cutting tools. In wheel bead cutting, CNC machines guide the cutting tools to trim and shape the wheel edges to exact specifications.
Advantages of CNC Machining
CNC machining offers several advantages over traditional manual machining methods:
- Precision: CNC machines can cut wheel beads with micrometer-level accuracy, ensuring a perfect fit for tires.
- Consistency: Once programmed, CNC machines produce identical cuts on every wheel, ensuring uniformity across batches.
- Efficiency: CNC machines can operate continuously, significantly increasing production speed and reducing lead times.
- Versatility: CNC machines can be programmed to cut various wheel designs and sizes, accommodating different vehicle types and customization requests.
The CNC Wheel Bead Cutting Process
Preparation and Setup
The CNC wheel bead cutting process begins with the preparation of the wheel and the setup of the CNC machine. This involves:
- Designing the Cutting Path: Using CAD (Computer-Aided Design) software, technicians create a digital model of the wheel and design the cutting path for the CNC machine.
- Programming the CNC Machine: The cutting path is converted into G-code, which is then loaded into the CNC machine's computer system.
- Mounting the Wheel: The wheel is securely mounted onto the CNC machine's rotating spindle.
Cutting the Wheel Beads
Once the setup is complete, the CNC machine begins the cutting process:
- Rotating the Wheel: The CNC machine rotates the wheel at a controlled speed.
- Cutting Tool Engagement: The cutting tools are precisely positioned to engage with the wheel's edge, trimming the beads according to the programmed design.
- Continuous Monitoring: Sensors and feedback systems monitor the cutting process in real-time, making adjustments as needed to maintain accuracy.
Quality Control
After the cutting process, the wheels undergo rigorous quality control checks to ensure they meet the required specifications. This includes:
- Visual Inspection: Checking for any visible defects or irregularities.
- Dimensional Verification: Using precision measuring instruments to verify the dimensions of the wheel beads.
- Performance Testing: Conducting tests to ensure the wheels fit tires properly and perform well under various conditions.
Applications and Benefits
Enhancing Aesthetics
CNC wheel bead cutting allows for the creation of intricate designs and patterns on the wheel edges, enhancing the overall aesthetic appeal of the wheels. This is particularly important for custom and high-end wheels, where visual impact is a key selling point.
Improving Performance
By ensuring a precise fit between the tire and the wheel, CNC wheel bead cutting contributes to better tire performance, including:
- Improved Air Retention: Reducing the likelihood of air leaks.
- Enhanced Stability: Providing a secure fit that enhances vehicle stability and handling.
- Increased Safety: Minimizing the risk of tire-related accidents.
Cost Efficiency
Despite the initial investment in CNC machinery, the efficiency and precision of CNC wheel bead cutting lead to long-term cost savings through:
- Reduced Material Waste: Precise cuts minimize scrap material.
- Lower Labor Costs: Automated processes reduce the need for manual labor.
- Faster Production: Increased production speed reduces lead times and increases output.
Conclusion
CNC wheel bead cutting represents a significant advancement in wheel manufacturing, combining precision, efficiency, and versatility. As the automotive industry continues to demand higher quality and more customized wheels, the role of CNC technology in wheel bead cutting is set to become even more critical. By leveraging the capabilities of CNC machines, manufacturers can produce wheels that not only meet stringent performance standards but also offer unparalleled aesthetic appeal, ultimately driving innovation and excellence in the automotive sector.
Bead cut on Alcoa style wheels 22.5" to 22" |
Bead cut on Alcoa style wheels 24.5" to 24" |
Milling cutom patterns strating at $$___ on new or used rims |
*All used rims must be SUPPLIED pressure washed clean and valve stems removed prior to work starting |
Share
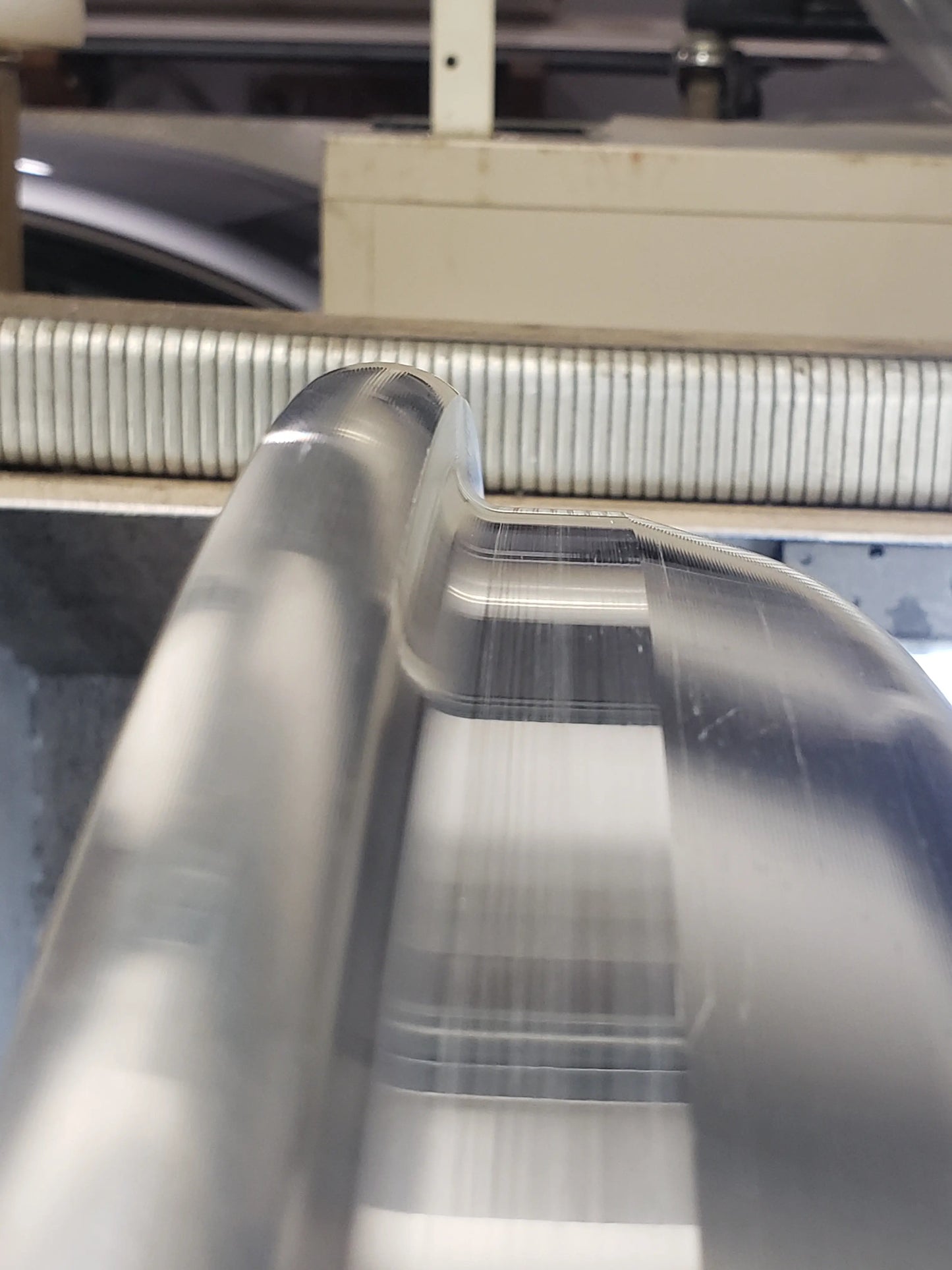
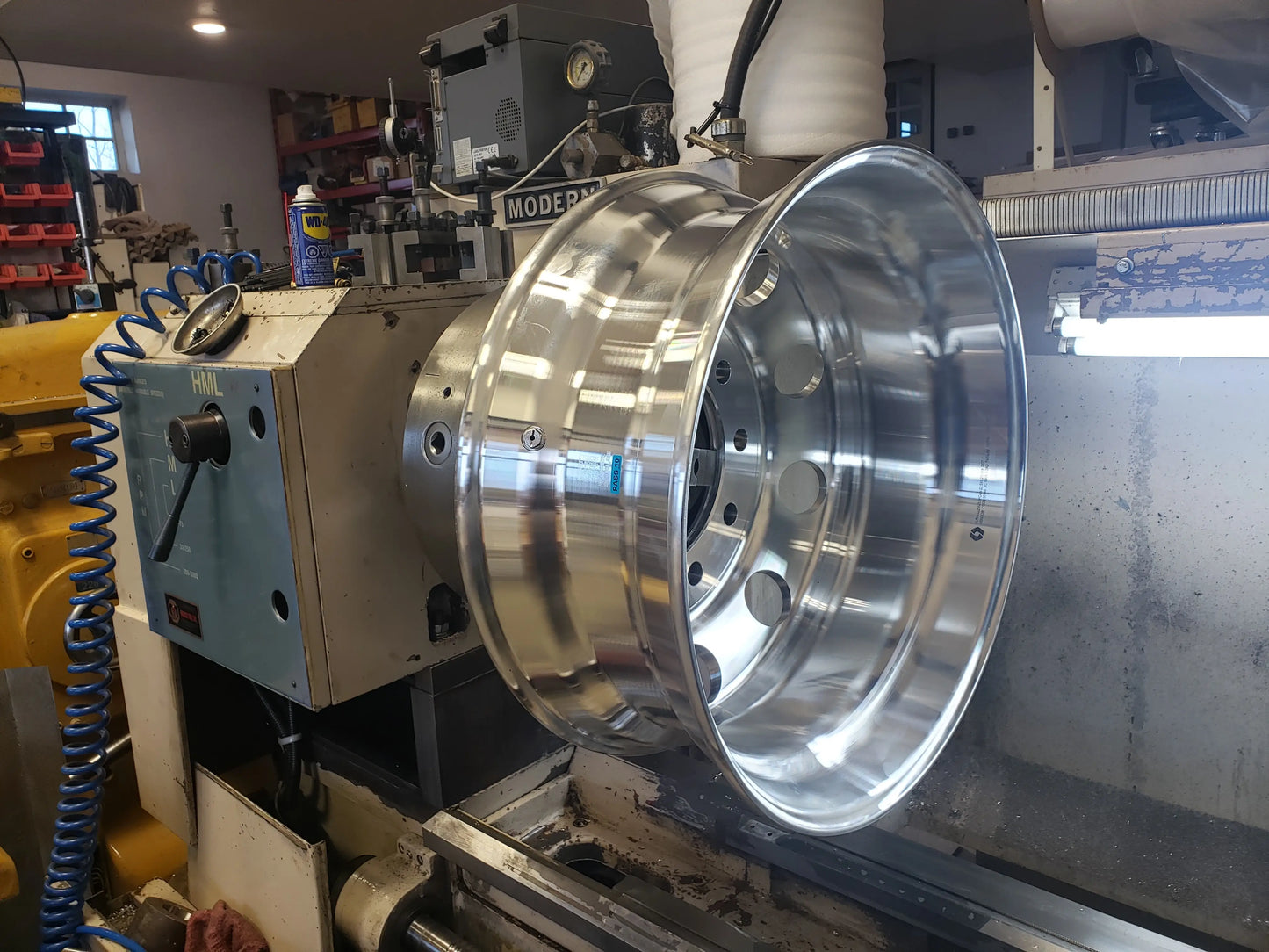
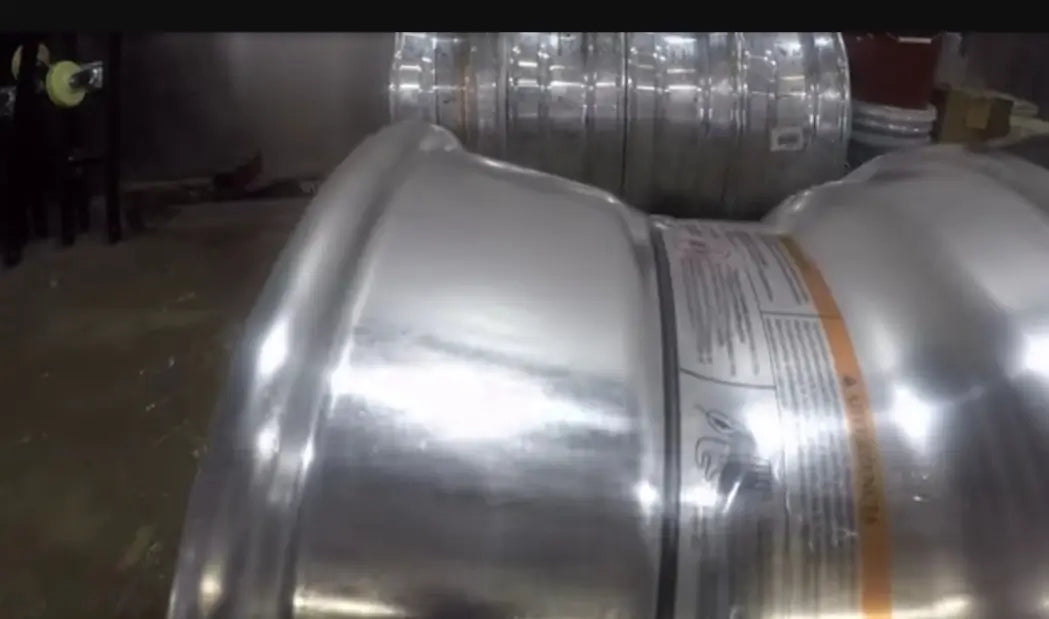
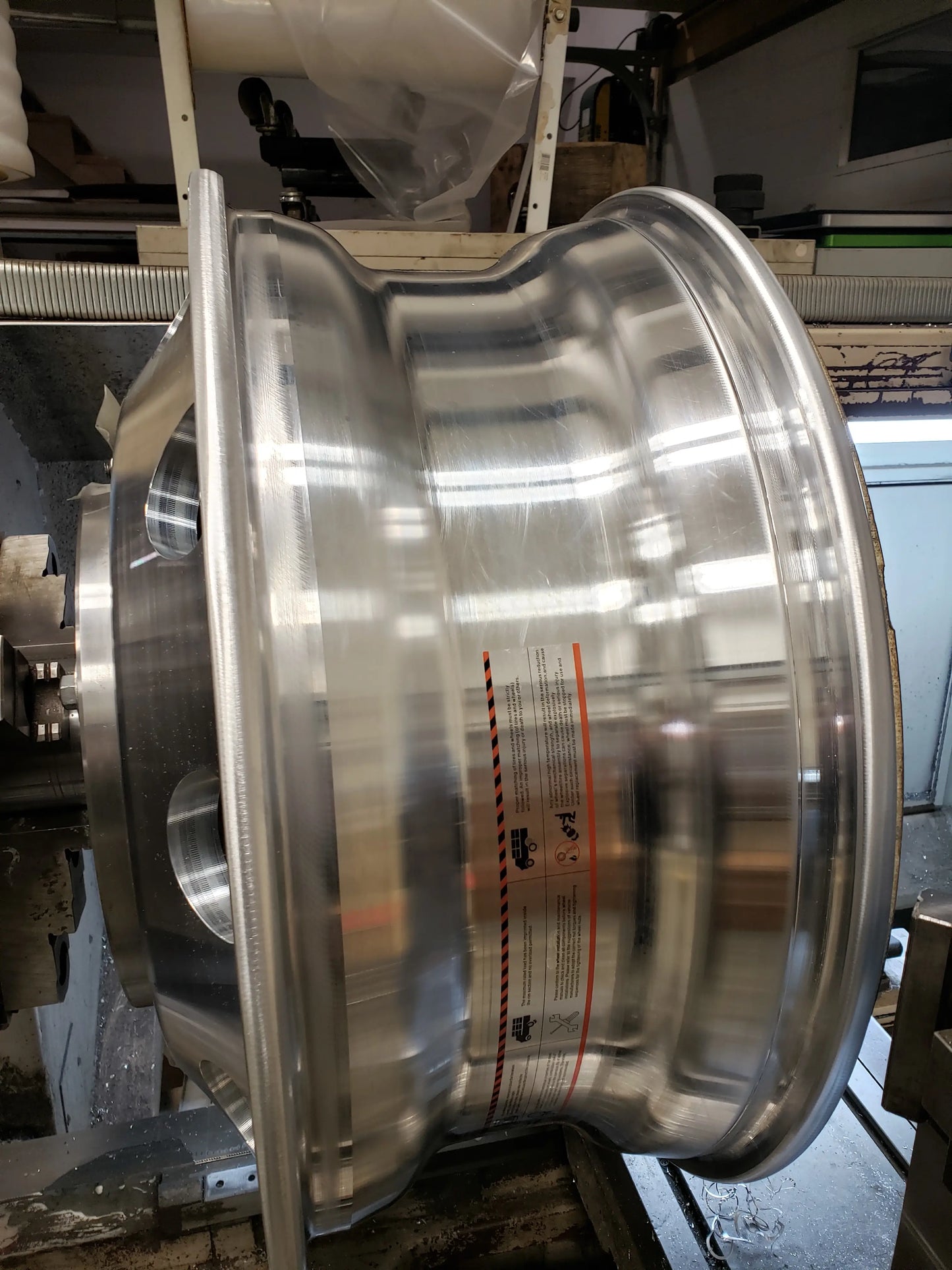
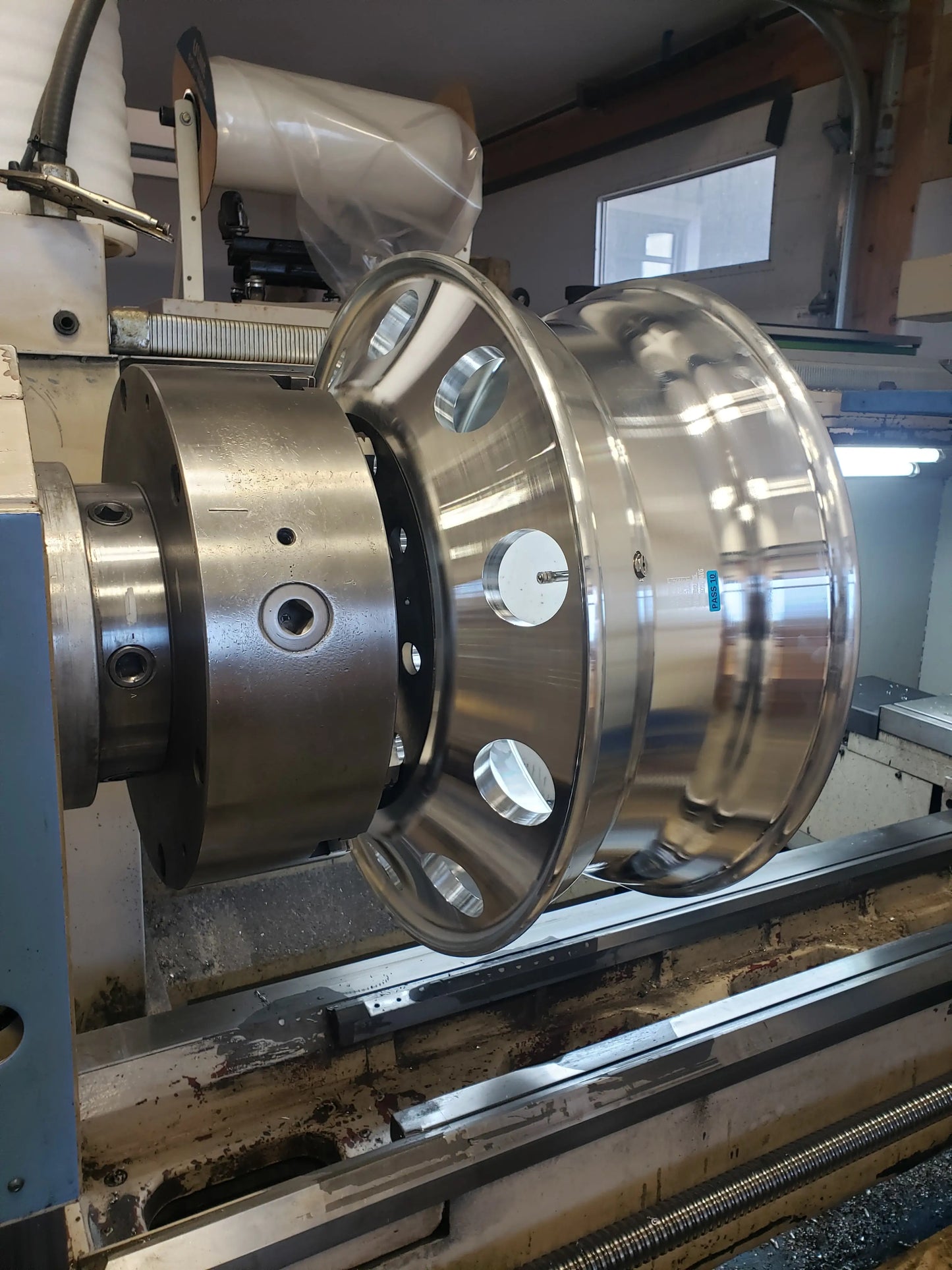
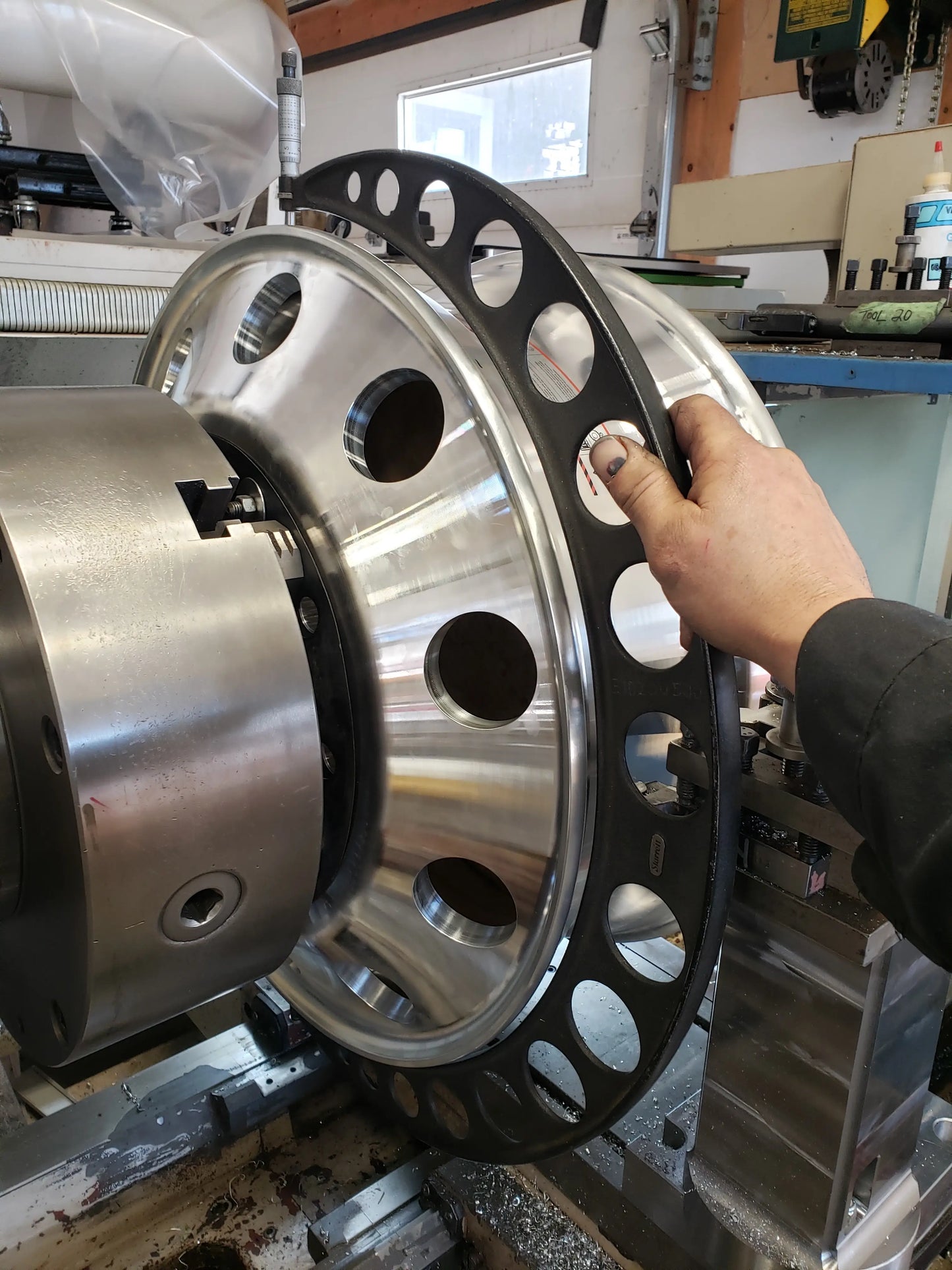
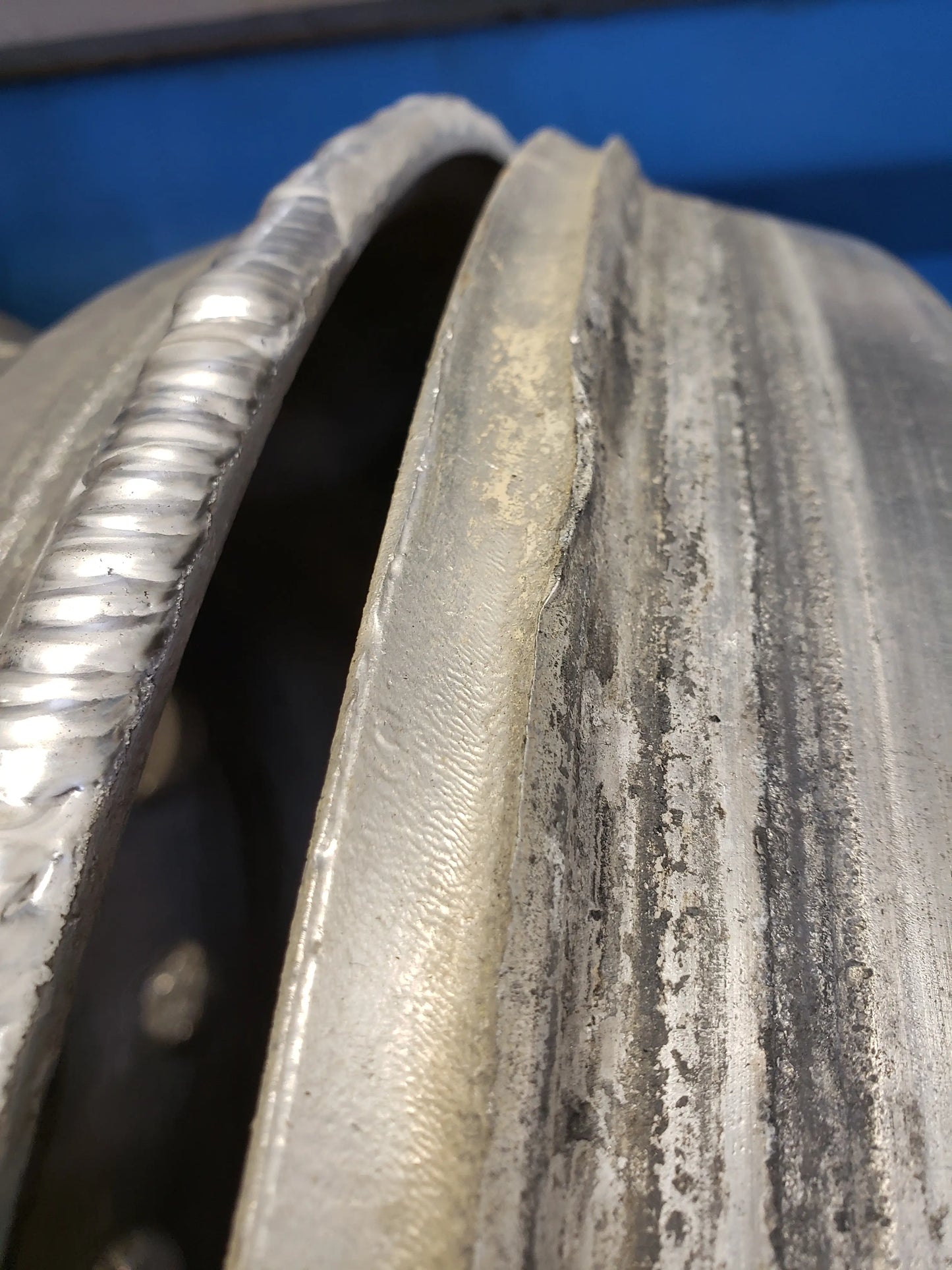
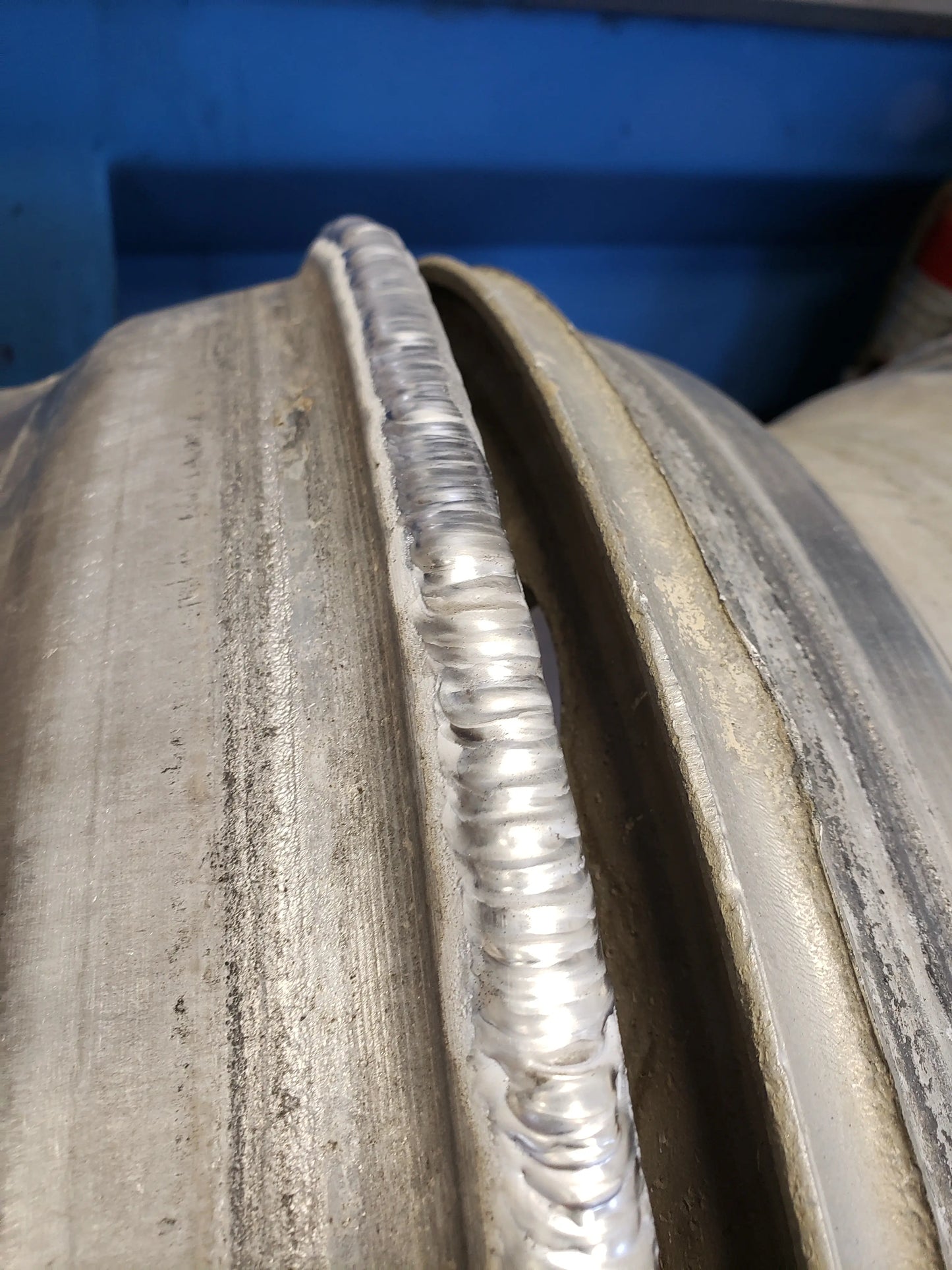
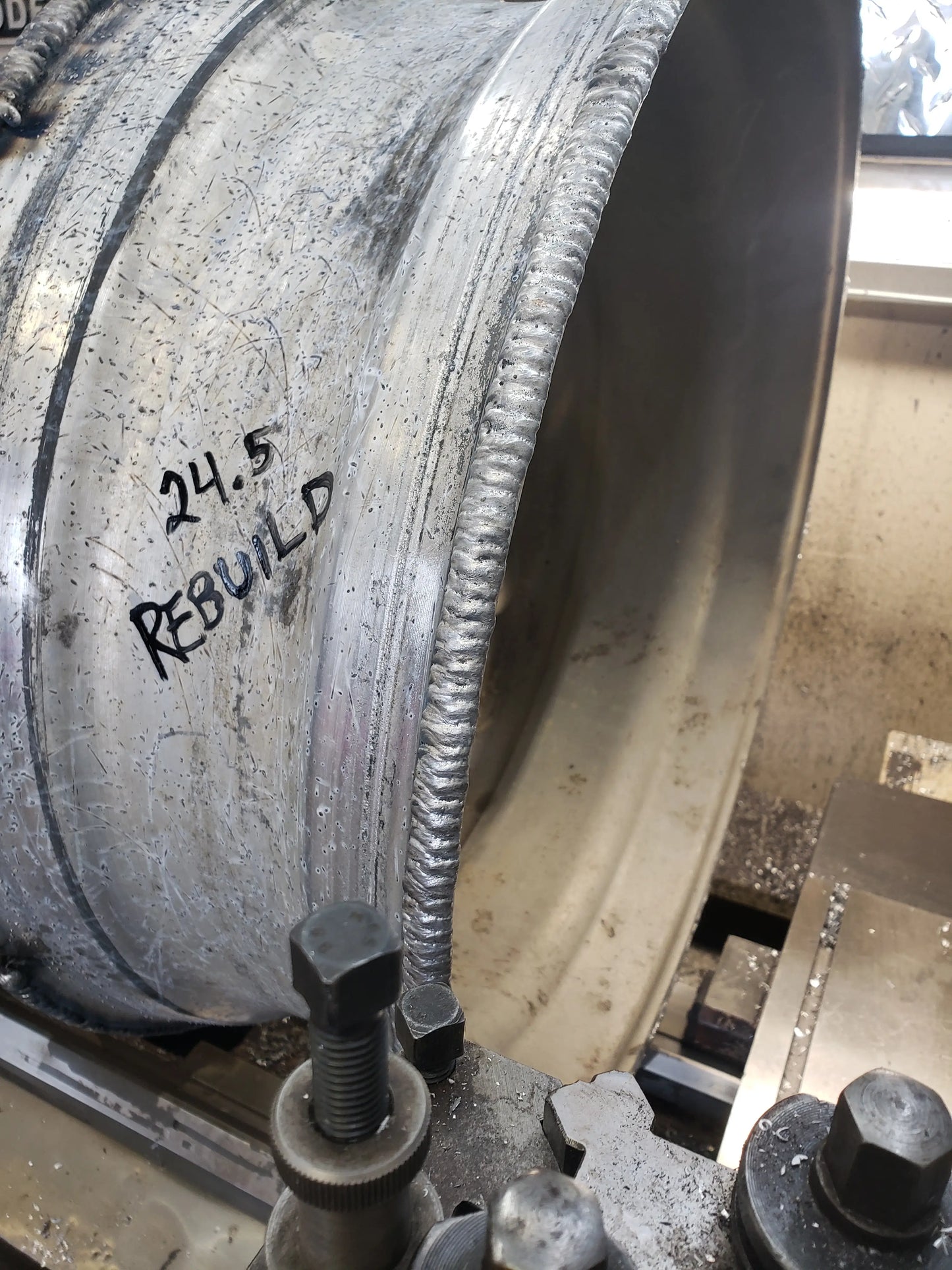

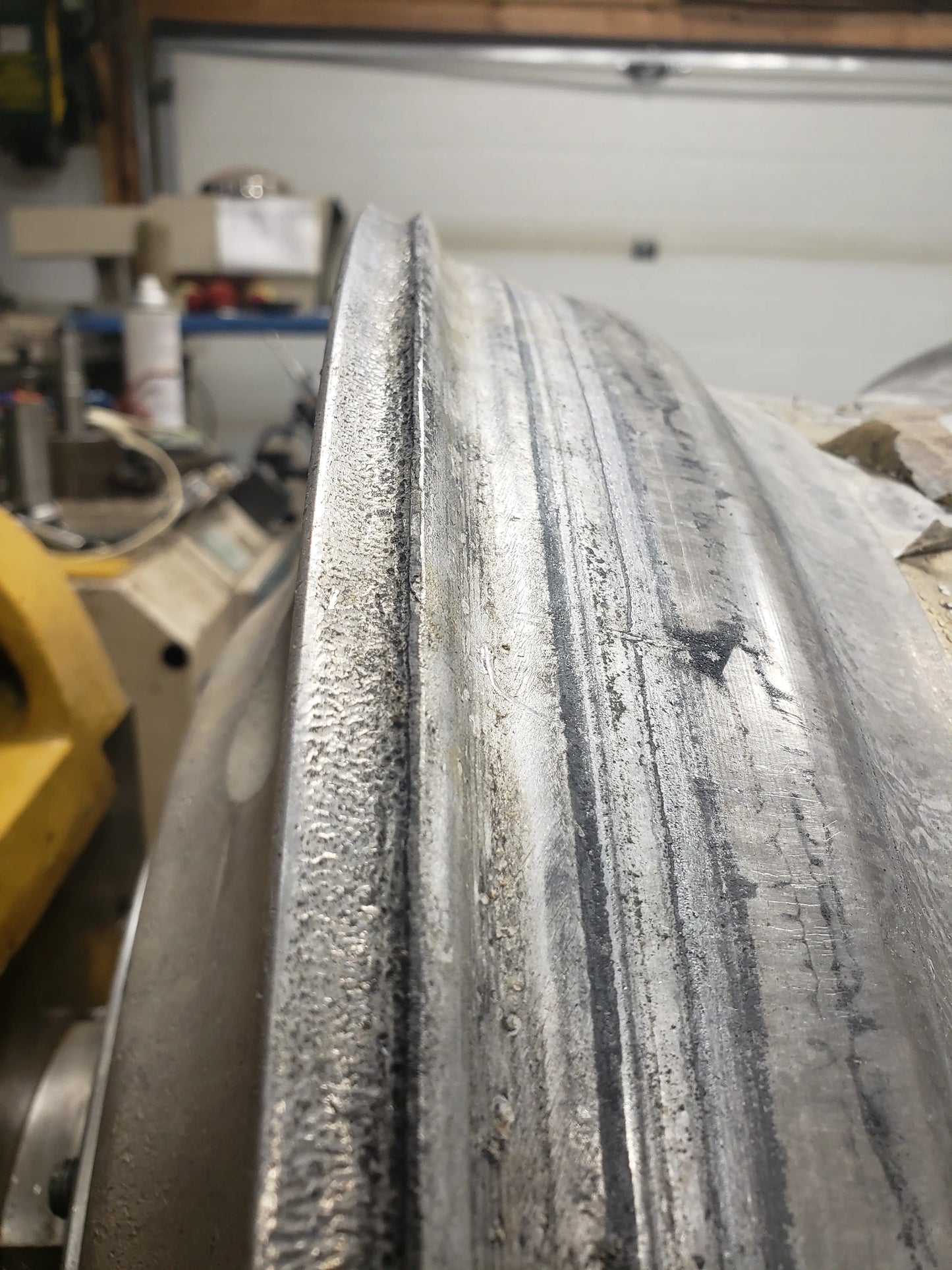
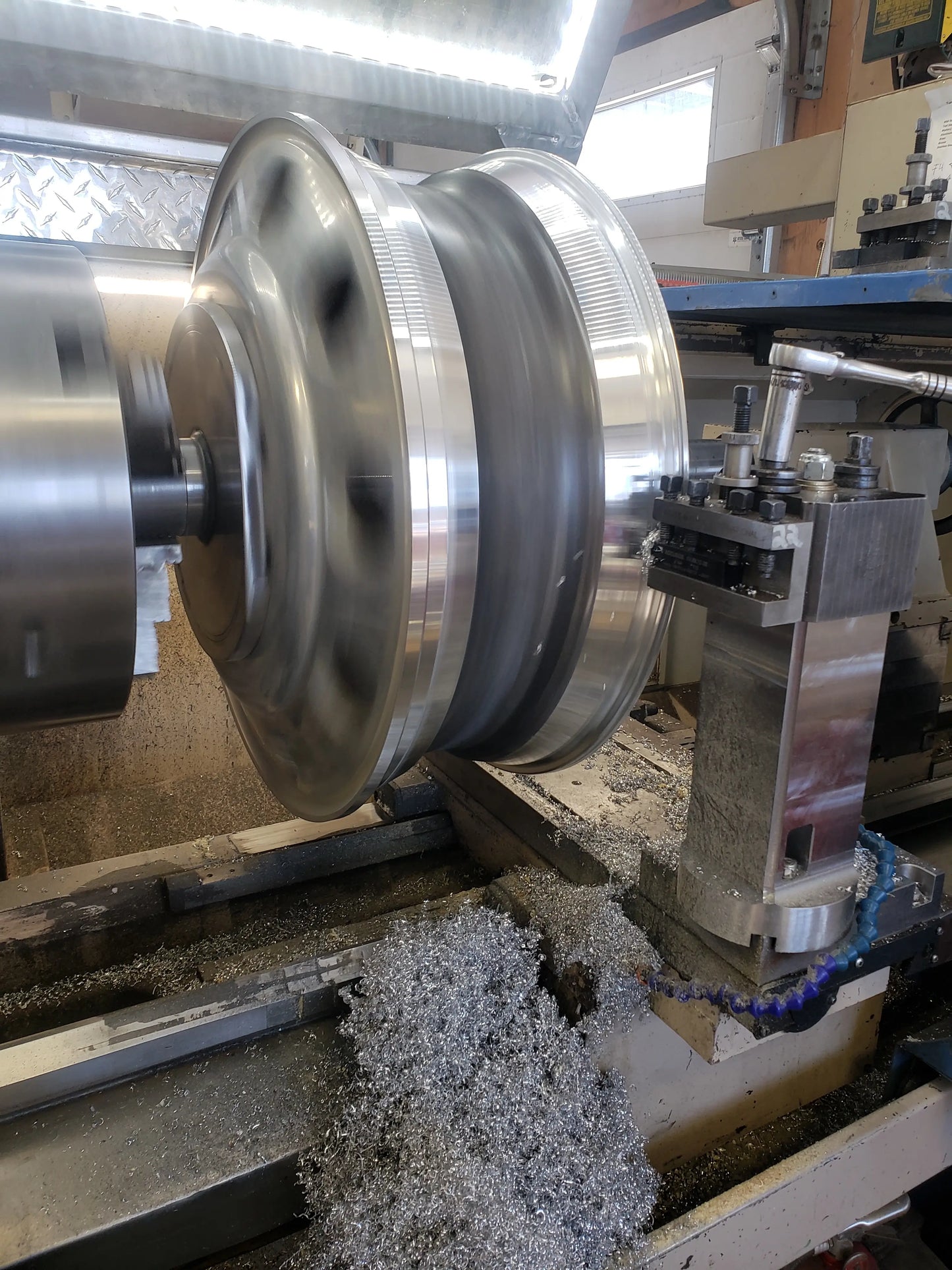
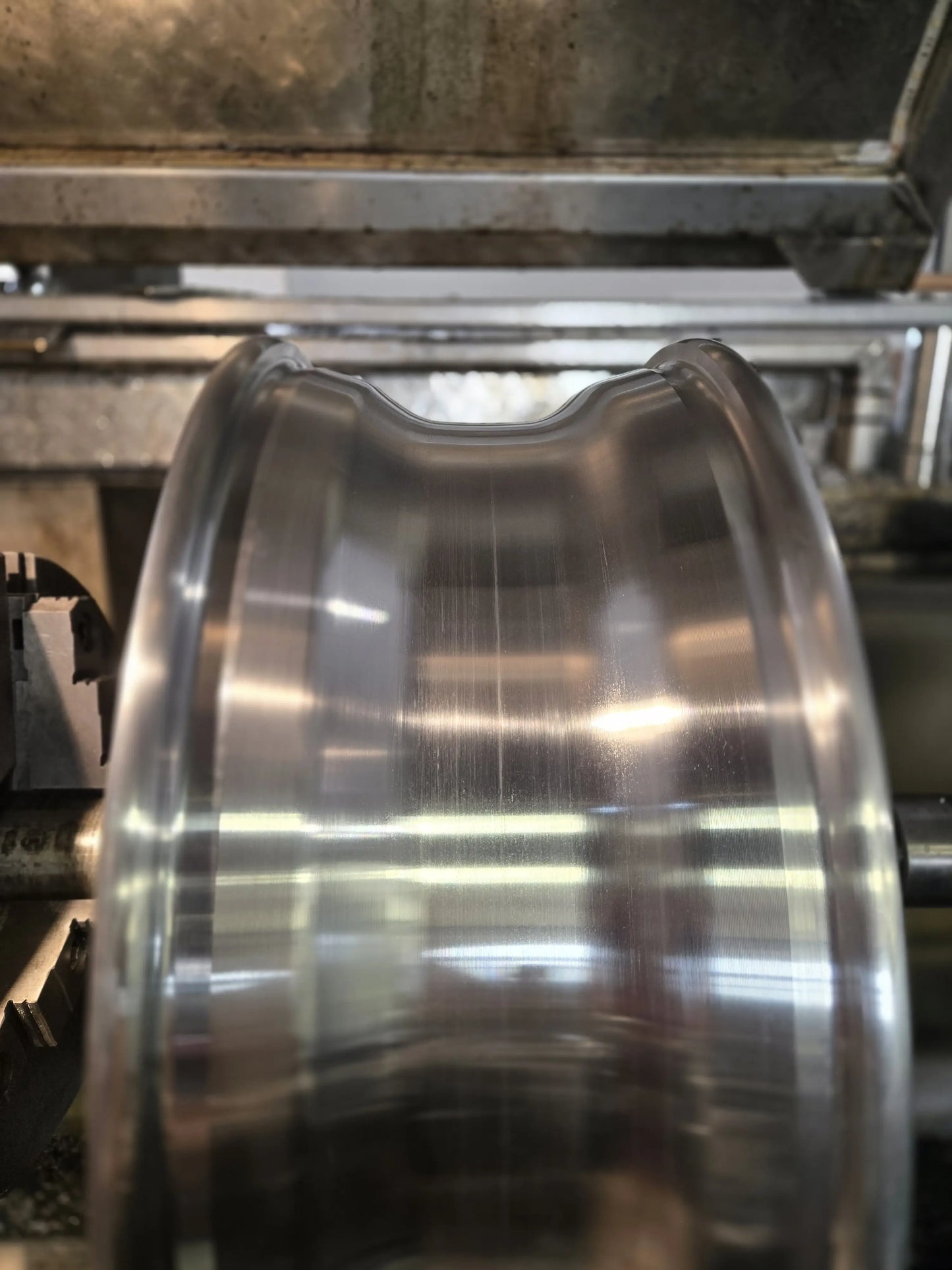
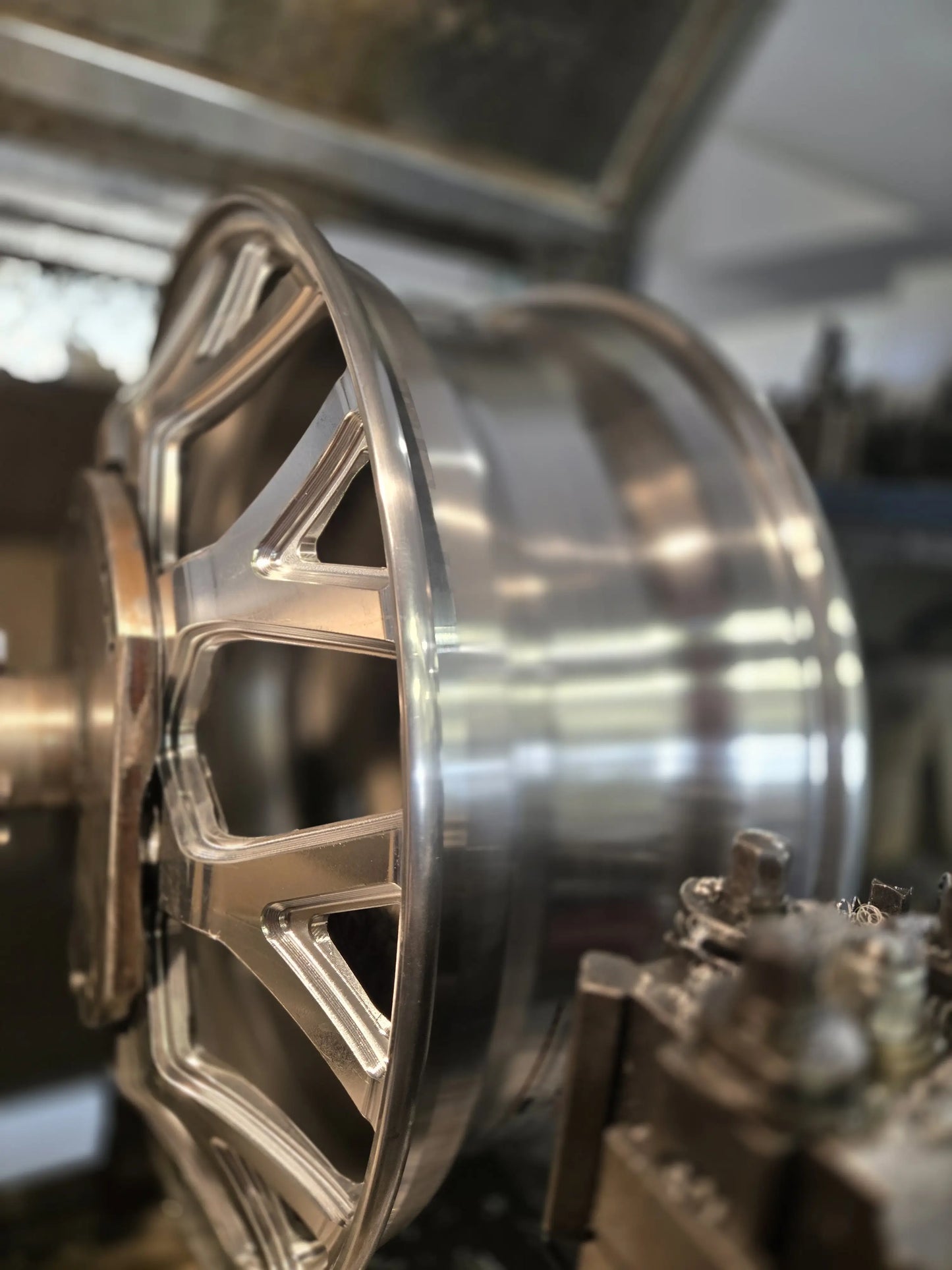
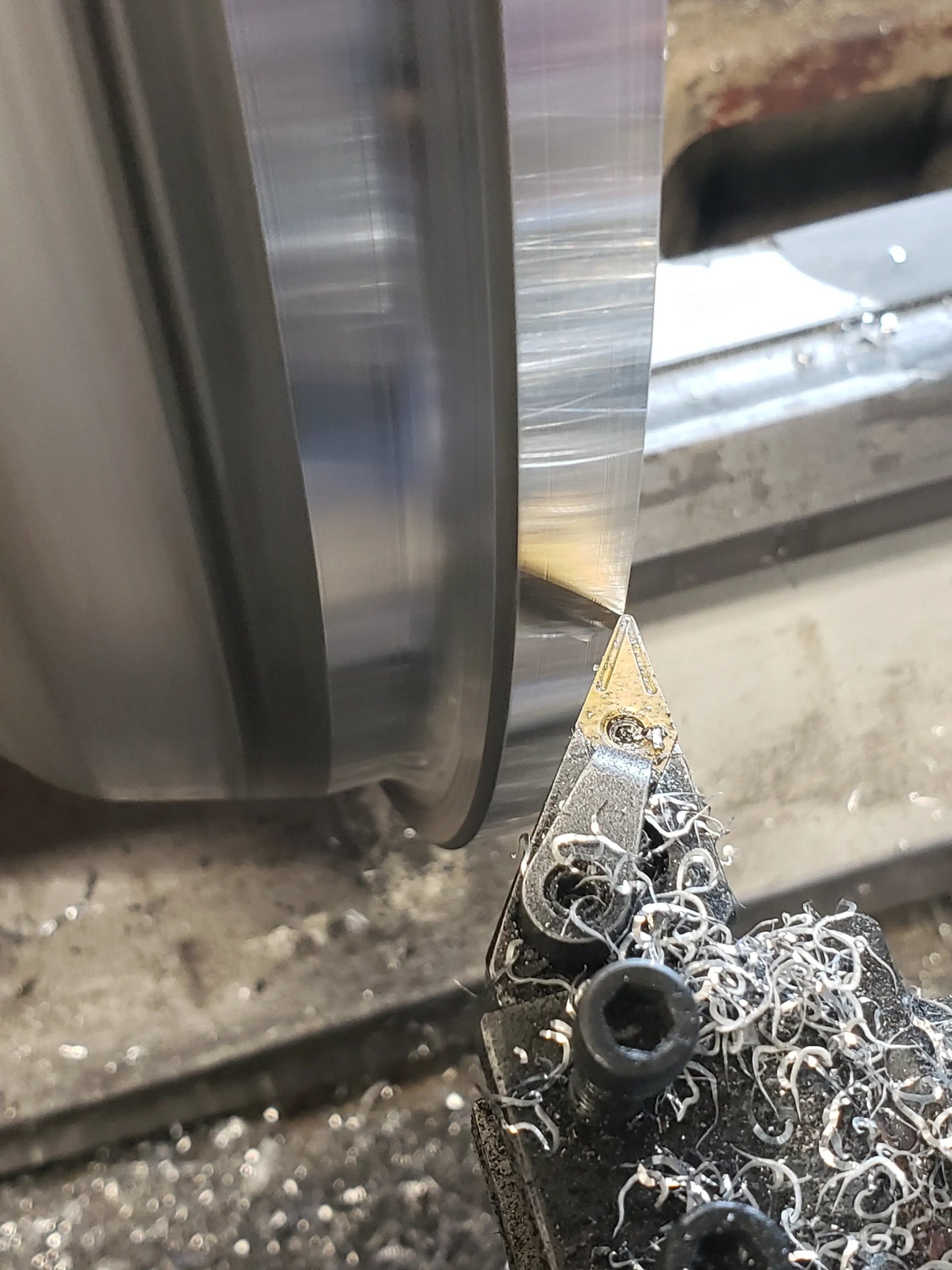
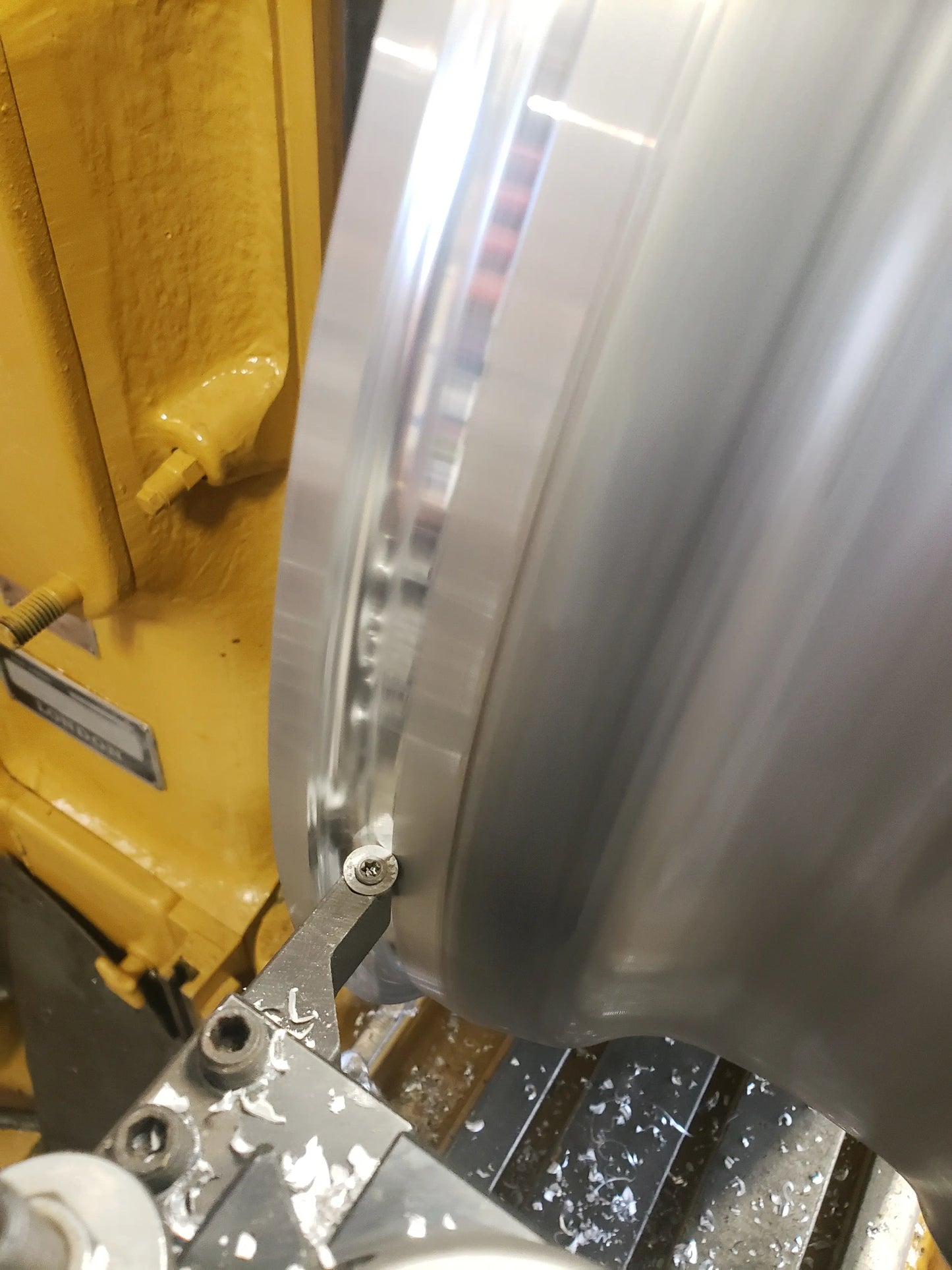
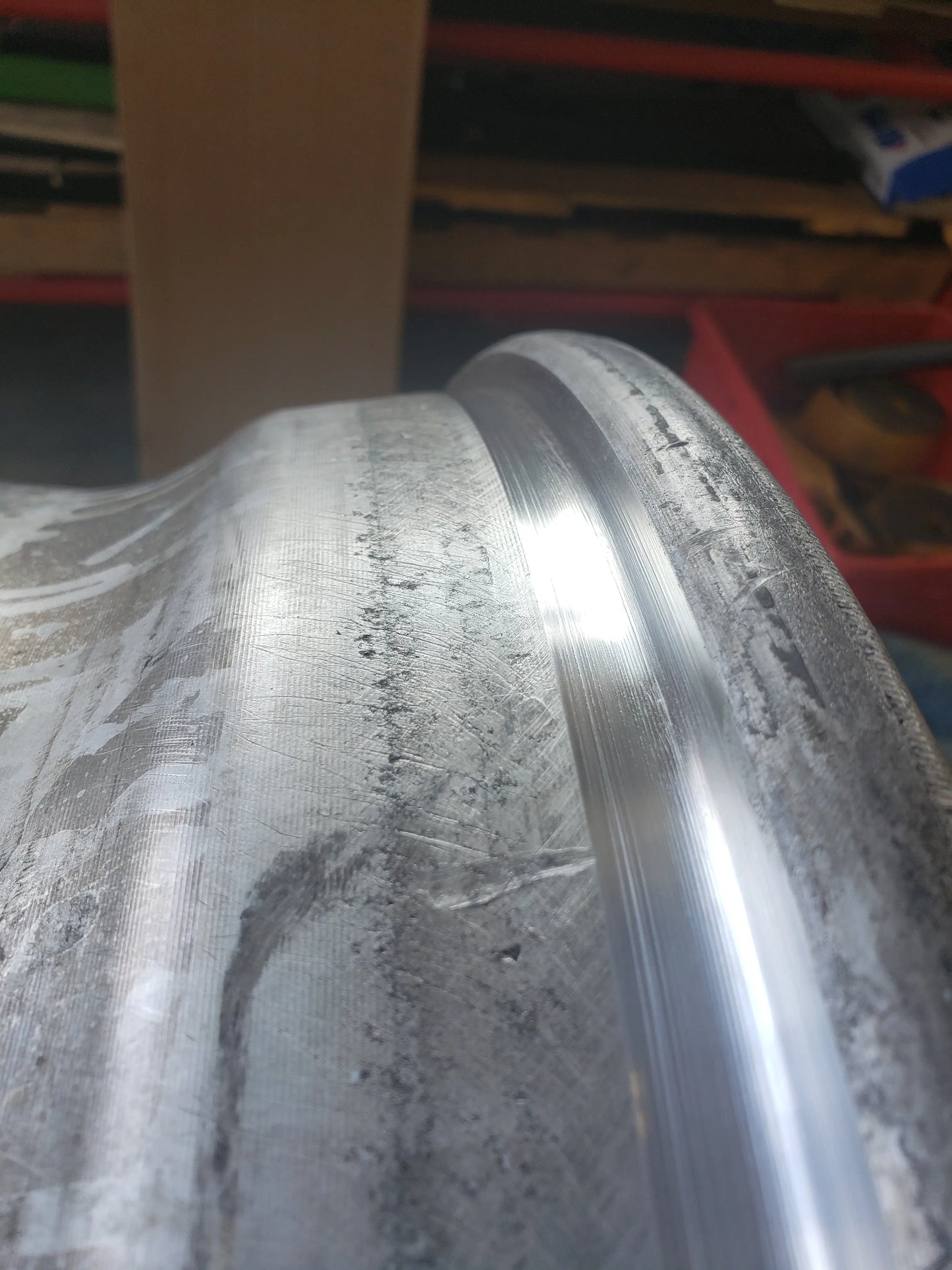